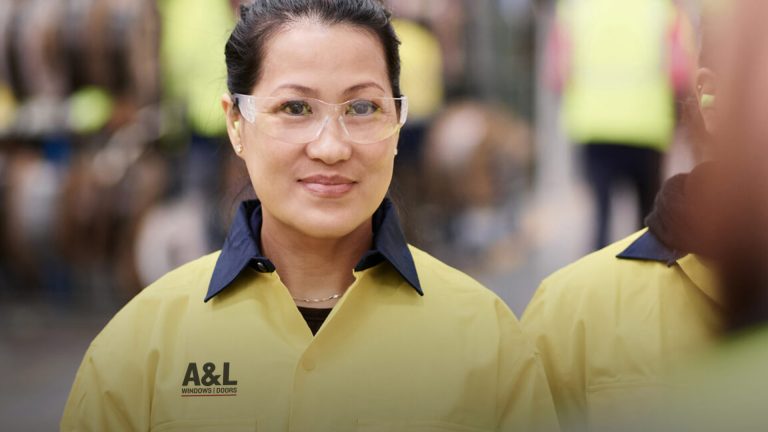
Locally made
The end goal is simple. ‘Quality’ is ensuring that every product is delivered as we intend and received as the customer expects. In other words, we put quality at the forefront of our thinking and processes, so you’re free to focus on other priorities.
While that sounds straightforward, it takes a variety of complex processes and procedures to ensure thousands of window and door products are manufactured and delivered to the highest standards every single day.
The best way to arrive at a high-quality outcome is to ensure quality is considered from the beginning. And then repeatedly throughout every step in the process that follows.
Rather than simply analysing the end results, our quality specialists are involved at every point, from the initial moment a product is just an idea or a sketch through to when it’s installed on site.
Whenever our teams begin to engage in research and design—whether of a product or a process—specialised quality coordinators are on hand and highly involved in the process.
It’s a holistic approach to design that involves input from multiple parties. Design and manufacturing teams will work with suppliers and customer representatives to question, discuss, and determine how certain aspects of a product should change or be configured, to ensure the most efficient production of high performing products.
Just because a product is ready for manufacturing at scale, doesn’t necessarily mean the design or quality assurance phase is complete.
Customer feedback is an ongoing, integral aspect of quality control and improvement over time.
Our teams actively source and request all kinds of feedback from clients and customers, whether it’s positive praise or opportunities for improvement.
Every piece of feedback we receive is categorised, analysed, and redistributed to the relevant team, to ensure we’re closely aligned with the reality of our customer’s requirements and expectations.
Quantitative data plays a critical role in the way we strive for quality.
Our teams maintain and review huge databases of information, which are used to pinpoint specific areas within processes or products that require further analysis or improvement.
Data not only helps to pinpoint any issues in the first instance; it also helps us to monitor whether corrective actions are effective in remedying the underlying issues to eliminate them in the future.
There are numerous varieties of information we can use to determine quality, depending on where the data comes from. We collect and inspect information relating to everything from transport and logistical information through to service support, to develop a comprehensive history of the actions taking place in relation to certain jobs, projects, or customer partnerships.
All of that data is highly visible throughout the business to ensure everyone across all of our teams has ownership and responsibility for the quality of what we produce.
It’s designed to create an environment where every team has access to the critical data that enables them to constantly hone and refine their approach.
Pinpointing problems is always beneficial, but the ultimate objective of the approach is to eliminate those problems and prevent them from recurring in future.
The most effective approach to minimising error and preserving quality involves a repeatable set of behaviours: when the process is set and replicable, teams can spend less energy determining a course of action and more time working to eliminate the issues.
Once an issue has been identified internally, there’s an almost automatic response from team members working to rectify the problem.
Once an issue is identified—at any point in the supply chain—the team’s immediate priority is to stop that issue from potentially escalating into any kind of larger concern.
When the issue is successfully contained, the team begin to map out what may be causing the problem.
Everyone contributes potential solutions or strategies for improvement, because everyone is responsible for the quality of our processes and production capability.
Eliminating the problem in the short-term is a priority, but improvement over time and preventative measures—supported by data and evidence—are the real benchmarks of success.